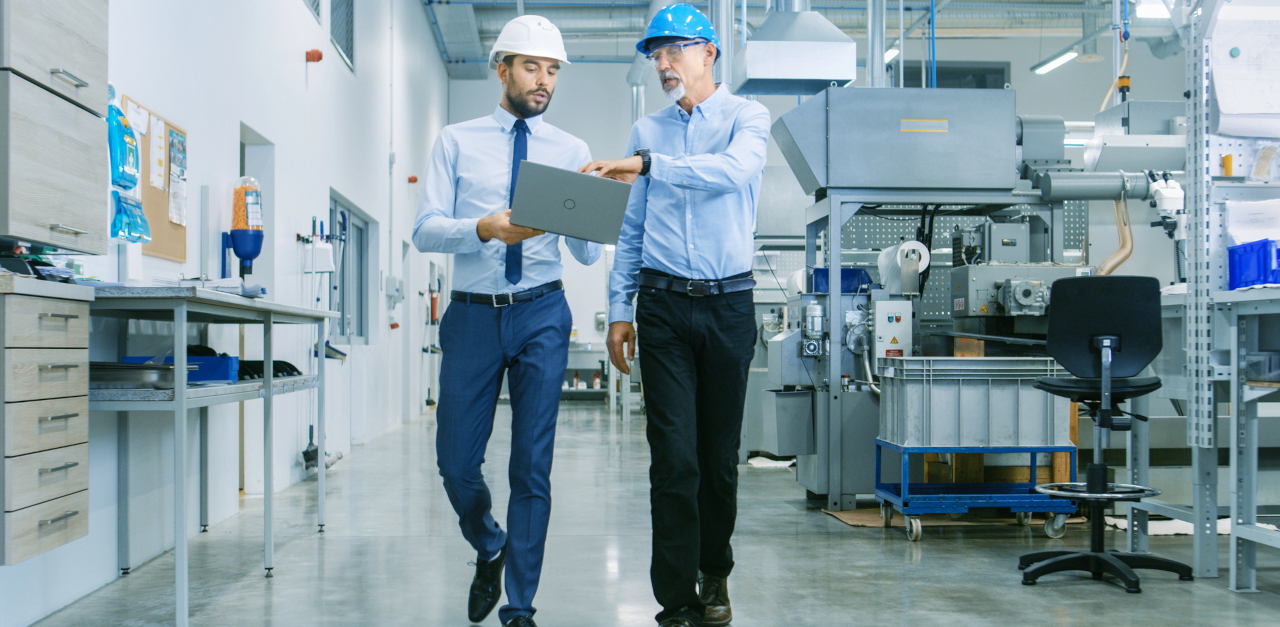
Manufacturing operations rely on complex machinery, tight schedules, and consistent output—so when something breaks down or slips through the cracks, the ripple effect can be costly. Asset-heavy environments like factories and plants face unique challenges that impact both productivity and profit.
- Unplanned downtime and equipment failures: Unexpected breakdowns bring production to a halt—and with every minute of downtime costing money, the pressure is on. Many manufacturers still operate reactively, without predictive tools that help catch issues before they happen.
- Lack of asset visibility and data: From machinery to support systems, manufacturers often struggle with siloed or incomplete asset data. Without a clear picture of asset condition, service history, and lifecycle costs, it’s hard to prioritise repairs, plan replacements, or make informed decisions.
- Inefficient maintenance processes: Manual scheduling, paper-based inspections, and disjointed systems slow everything down. Maintenance teams waste time chasing parts, paperwork, or approval—when they could be focused on keeping production running smoothly.
With the right Enterprise Asset Management (EAM) tools, manufacturing teams can shift from reactive to proactive, reduce downtime, and make smarter decisions based on real data.
What’s keeping you up at night? Let’s talk